Coir rope industry faces tough future
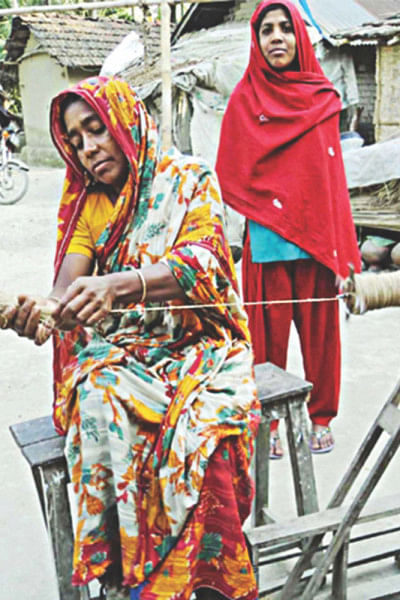
Centuries ago, when Indian navigators sailed to Malaya, Java, China and Arabia, they did so using coir ropes. Coir is the fibre of coconut shells; and in Jessore's Monirampur upazila the production of coir ropes is a traditional industry that has survived into modern times. Sadly, it's become an industry with an uncertain future.
“Making rope used to be very inexpensive,” says one rope-maker, Yusuf Ali from Rajgong village in Chaluahati union. “We were able to collect fallen coconuts from the roadsides for free, so really there wasn't any cost at all. In years gone by there was good demand for Jessore ropes.”
Traditionally, among the thousands of rope-makers in the area were a good number of housewives. Being able to work from home and earn up to Tk 300 per day, they found rope manufacture appealing. But times have changed.
“These days, a hundred coconut shells costs around Tk 300 in the market,” says another rope-maker, Abdul Wadud. “That means to make four kilograms of rope we have to spend nearly Tk 800 upfront.”
The industry's challenges aren't limited to the higher cost of raw material. The availability of heavy nylon and other synthetic ropes has brought new competition to coir ropes, with the traditional industry now at risk of being lost altogether.
In traditional rope-making villages like Khatoyadanga and Amrajhuta, many villagers have already given up the customary trade in favour of more reliable work as day labourers and rickshaw drivers.
Yet some persist. There is an emotional attachment: rope-making is often thought to be a kind of a living link with their ancestry; and spirits are buoyed by the knowledge that coir ropes still hold advantages over synthetic alternatives for some uses.
“Coir ropes are very strong,” explains Fazr Ali, a rope trader from Rajganj Bazar. “They are most often used to keep nipa palm roofs in place. They are suitable for traditional homes and garden pavilions, as well as for securing paddy stacks.”
Comments